Cycle time (CT) is the time a scrum team takes to make a product. On the other hand lead time (LT) is the time taken by a team from receiving the order till the end product is delivered. CT is always shorter than LT. In this blog, the main focus is directed towards the difference between LT and CT.
The difference between CT and LT
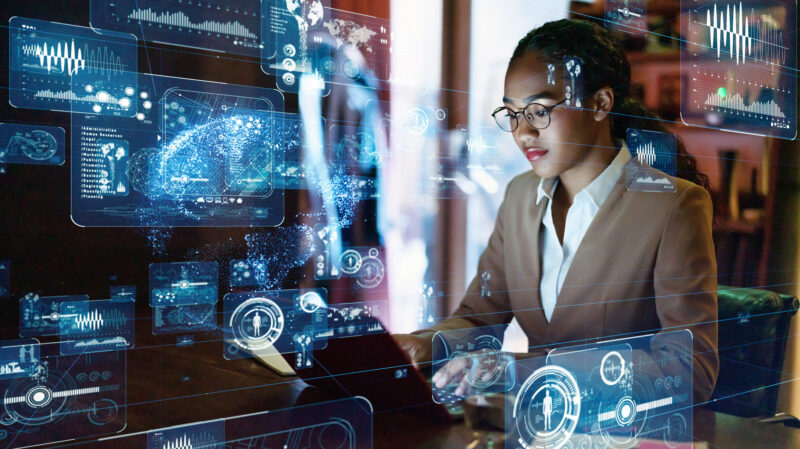
The CT is the amount of time needed by a team to complete the work. It also includes the rework that the project has undergone. It starts when the work is in progress and the end is when the project is marked as done.
LT is the time taken to make the product and ship it. It is the time from when the order is received from the customer and the moment when it reaches the customer.
CTs help to mark the areas that need to be worked on. It helped the team to improve the efficiency and do the work without committing any kinds of silly mistakes. LT helps you to keep track of the products falling into your queue and tick them off from your list.
To put it more easily, LT is the time taken to produce a product while CT is the estimated time that one will require to manufacture the product.
There are also some similarities between LT and CT. Without any further ado, delve deeper into the differences here.
Similarities between LT and CT
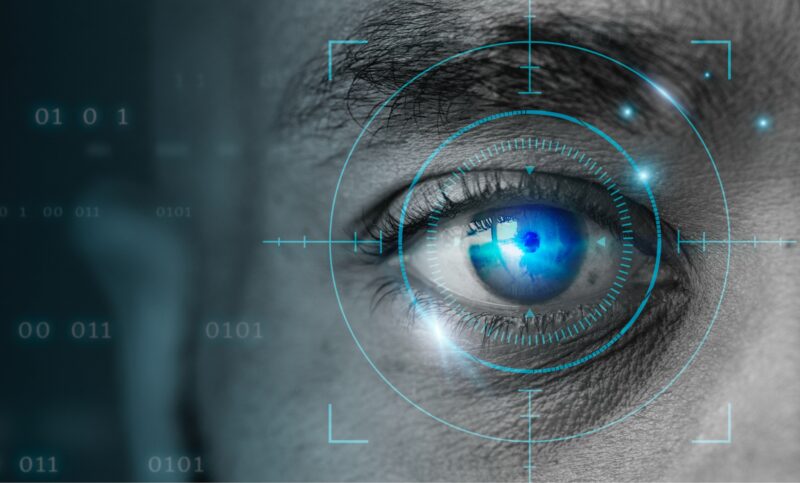
Both time cycles are measured in minutes, days, weeks or months to complete the final product. It is the time taken for a product to reach the endpoint from the starting point.
Both units give an idea to the team about how they need to plan for the future. Both units miss a similar point, human management.
Also, they are great at predicting any kind of issue the team might face in the upcoming projects.
LT and CT are two important concepts in various industries, especially in manufacturing, logistics, and project management. While they may sound similar, they represent different aspects of the production process. In this article, we will delve into the definitions and significance of LT and CT, as well as their differences and how they impact businesses.
Let’s start with LT. Lead time refers to the duration between the initiation of a process or an order and its completion. It includes all the necessary steps and activities required to fulfil a request or produce a product, from the moment it is requested to the moment it is delivered. LT encompasses the time spent on procurement, manufacturing, quality control, transportation, and any other relevant processes.
LT is a critical factor for businesses as it directly impacts customer satisfaction, inventory management, and overall operational efficiency. A shorter lead time allows companies to deliver products or services faster, which can enhance customer experience and increase customer loyalty. Additionally, reducing lead time can help businesses minimize inventory levels, as they can operate with smaller buffers and respond more effectively to changing demands.
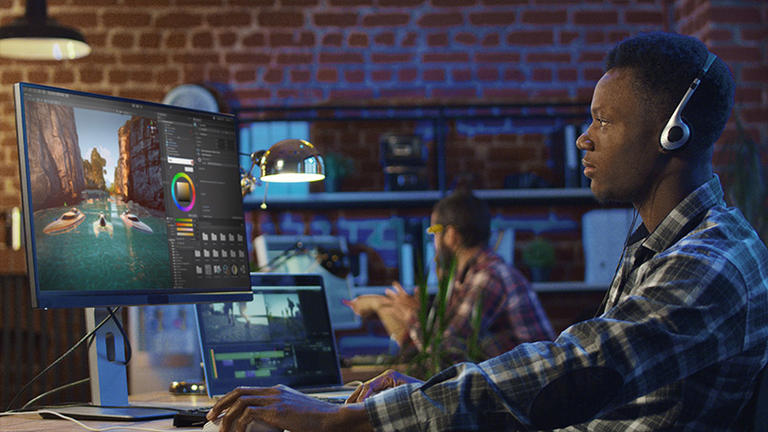
On the other hand, CT refers to the time required to complete one cycle of a process or operation. It measures the efficiency of a specific step or activity within the overall lead time. CT focuses on the duration of a single unit’s processing or production, from start to finish. It excludes any waiting and idling and concentrates solely on the active work time.
CT is crucial for identifying bottlenecks, optimizing processes, and increasing productivity. By analyzing cycle times, businesses can identify areas of improvement, streamline workflows, and reduce unnecessary delays or interruptions. It allows organisations to set realistic production targets and identify potential constraints in their operations, enabling them to make informed decisions and allocate resources more effectively.
While LT and CT have distinct meanings, they are interconnected. LT is the sum of all the individual cycle times involved in a process. By optimizing these CTs, businesses can reduce overall lead time and achieve greater operational efficiency.
To effectively manage LT and CT, organisations can implement various strategies and methodologies such as Lean manufacturing, Six Sigma, or Agile project management. These approaches focus on identifying and eliminating waste, improving processes, and enhancing productivity through continuous improvement initiatives.
Furthermore, technology plays a crucial role in reducing LT and CT. Automation, data analysis, and real-time tracking systems can provide valuable insights into the production process, enabling businesses to identify areas for improvement, monitor performance, and make data-driven decisions. By leveraging technology, companies can achieve higher accuracy, faster turnaround, and improved customer satisfaction.
Conclusion
LT and CT are key metrics that businesses need to understand and manage effectively. While LT represents the total time from order initiation to delivery, CT measures the time taken to complete a specific process or operation. By optimizing CTs, companies can reduce lead time, enhance customer satisfaction, and improve overall operational efficiency. Implementing strategies such as Lean manufacturing and leveraging technology can aid in achieving these objectives. Understanding and actively managing LT and CT are vital for businesses to stay competitive in today’s fast-paced and demanding market.
Often people confuse LT and CT. However, they are totally different and CT is much more important than LT. The project managers and in charge are fully aware of tier difference and take insights that these two provide them while working on a project. These units are also helpful as the team get a clear vision of how to work for the future projects.